...Німцям потрібно 17 днів, а українцям цілий рік, щоб виготовити один і той же об’єм продукції.
І про економічний розвиток можна забути, якщо ми не зможемо зменшити ці відставання. Звичайно це проблема, але не вирок.
З подібною проблемою колись зіткнулись японці. Перед початком Другої світової війни продуктивність праці в Японії була дуже низькою. Співвідношення продуктивності праці японців і американців складало 9:1. Тобто, потрібно було 9 японців щоб виготовити такий об‘єм продукції, який виробляв всього 1 американець за одиницю часу.
І тоді японці почали задаватись питанням. Невже американці витрачають в 9 раз більше зусиль чи рухів, щоб виконати якусь роботу? Звісно ж ні.
Значить це японці неефективно використовують свій робочий час. І вони почали шукати відповіді як вирішити цю проблему.
В процесі цього пошуку було ідентифіковано ряд проблем, які впливають на зменшення ефективності (приклад на картинці). І були розроблені способи їх вирішення.
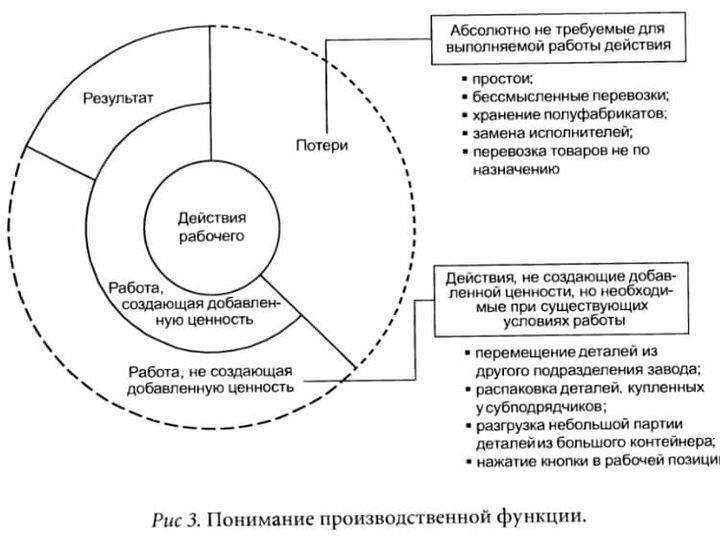
Так з’явилась славнозвісна Тойота Продакшн Систем (ТПС), яка в свою чергу еволюціонувала в систему «ощадливого виробництва» і згодом завоювала світову популярність.
Знаєте, нам як японцям не потрібно зараз придумувати заново велосипед. В світі є велика кількість інструментів, які можуть допомогти збільшити ефективність. Було б тільки бажання їх впроваджувати.
9 днів - саме стільки часу займає процес кінцевої збірки Боїнга 737. Ще 3 тижні необхідно для тестування і випробувань літака.
Коли почув цю цифру, то мені одразу згадалась моя екскурсія на завод Антонова, де мені розповідали, що строк будівництва літака складає 1,5 року.
Один місяць в США та півтора року у нас. Доречі, саме ця наочна демонстрація провалля в продуктивності праці в наших компаніях та західних.
Чому така величезна різниця? Тут існує декілька пояснень.
У будь-якому виробництві дуже велику роль грає безперервність самого виробництва, яка в свою чергу впливає на криву навчання - learning curve. В класичному розумінні ця крива значить, що при збільшення часу, досвіду та кількості спроб, паралельно зростає продуктивність праці.
Пояснюється це дуже просто на прикладі нашої компаніі. Коли українська компанія має одне замовлення в рік, то в неї немає налагодженої системи поставок та довгострокових контрактів з постачальниками. І вони одразу починають хаотично шукати комплектуючі. По всьому світу. Після того як знайдуть, то для початку їм потрібно узгодити і підписати новий контракт -це займає час. Узгодити форму фінансування та знайти джерела фінансування - це також час. Дочекатись коли постачальник виготовить та поставить деталі - і це також час.
Коли в компаніі немає постійних замовлень, то там також не існує необхідності організації робочого процесу. Працівники можуть годинами пити каву та курити. Сам виробничий процес може затримуватись поставки інструментів та комплектуючих. Доречі, в таких умовах нестабільних замовлень ніхто не буде тримати запаси сировини та комплектуючих, бо невідомо коли буде замовлення і яке воно буде. Комплектуючі можуть бути для одного продукту, а замовлять інше. Якщо ж номенклатура кількості товарів досить широка, то забезпечення деталей необхідної кількості необхідно буде заморозити значну частину коштів на невідомий термін та ще й при неорганізованому виробництві це може створити хаос в запасах.
Спішити їм нема куди, бо оскільки такі компаніі як Боїнг та Ейрбас перезавантаженні замовленнями, то вони теж його виконають не раніше ніж через рік-півтора.
Однак, всі ці проблеми, які в минулому впливали на зростання терміну виробництва, можна і треба вирішувати. Було б лише бажання це зробити.